PCB in dispenser machines
Advantages of using a smart infrared sensor checking the temperature of the PCB in dispenser machines
This Fortune 200 global industrial manufacturer operates in 58 countries, and develops and provides capital equipment used in electronics manufacturing. These can be found in premier printed circuit board (PCB) assembly facilities worldwide. In one of their fluid dispensers, they were running into a thermal management challenge and were looking how to control the temperature of the PCB. To give you an idea of the size of the PCB market, this was $75 billion in 2021 and knows a CAGR of over 5% of which the electronics industry covers a larg part of this market.
Dispensing technology
Dispensing is a process in which glue, oil or other liquids are applied or dripped to a PCB or specific components mounted on a PCB. Materials dispensed can range from very low (water like) to very high (toothpaste like) viscosity and encompass many different functions. These include solder paste to electrically connect components, encapsulants to protect devices from atmospheric conditions and provide moisture-proof insulation, thermal interface materials (TIMs) to help dissipate heat from parts, and adhesives to attach parts to a substrate or assembly. The dispensing process actually is a process to protect the product and improve the product reliability.
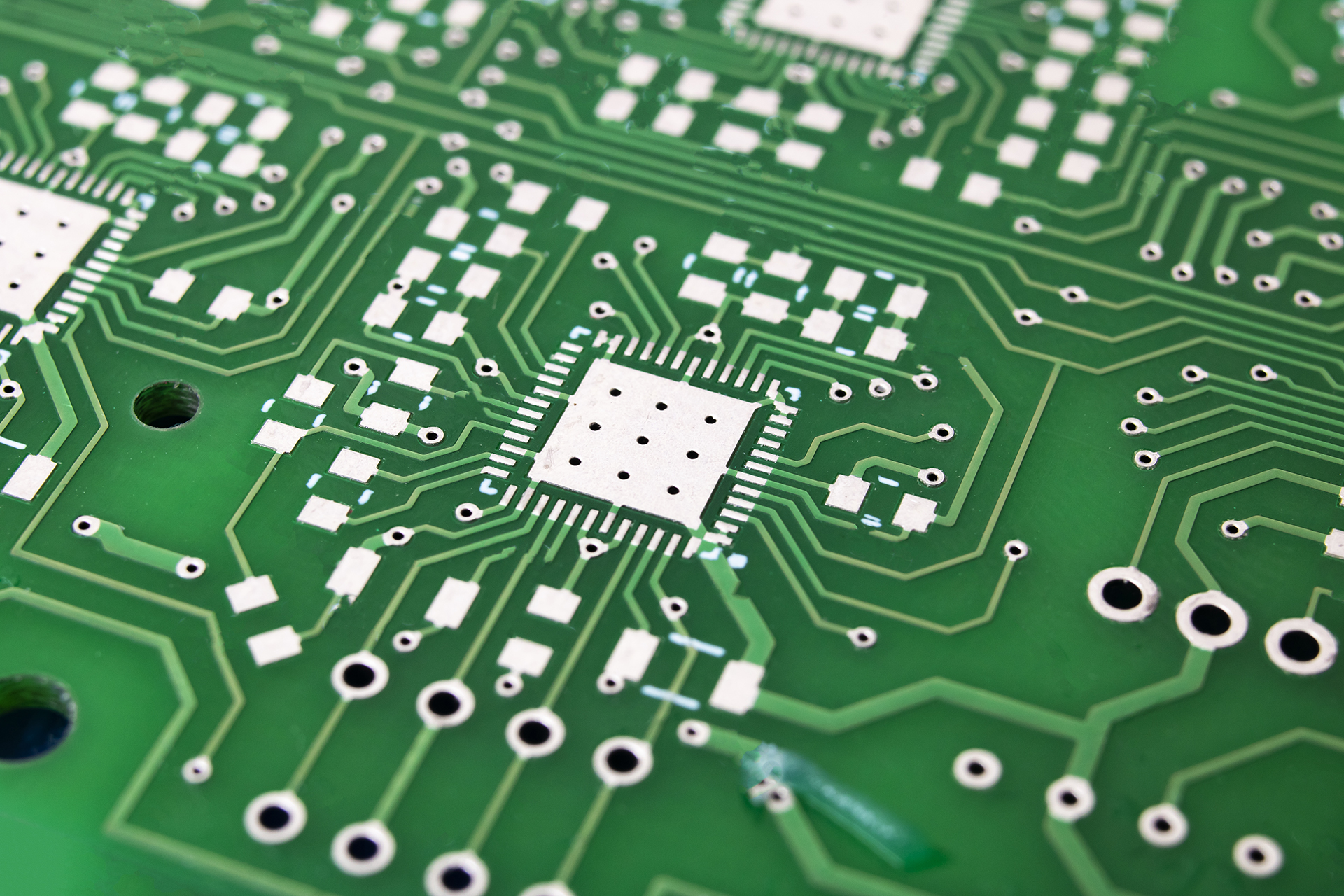
As an example, dispensing is used to prevent solder joints from loosening, especially in areas of weak structure on the PCB, such as chips. When the product falls and vibrates, the PCB will vibrate back and forth, and the vibration will be transmitted to the solder joints between the chip and the PCB, which will crack the solder joints. At this time, dispensing does make the solder joints completely surrounded by glue, reducing the risk of cracking in the solder joints.
One technique used to fixate chips on PCBs is called underfill. In underfill applications, a precise volume of underfill material is dispensed along the side of a chip or package to flow underneath through capillary action, filling air gaps around solder balls that connect chip packages to the PCB or stacked chips in multi-chip packages.
Nowadays, more and more companies have put forward higher-level requirements for the usability and stability of electronic products which positioned the dispensing technology in PCBA as an indispensable procedure.
Why temperature is critical
In dispensing processes temperature is critical in several ways: temperature effects the viscosity of the glue, resin or adhesive that is applied. Viscosity subsequently affects flow rates and spot or line sizes of the dispensed material. Lower temperature means lower viscosity, lower flow rates and bigger lines or spots, and vice versa. Manufacturers of adhesives will specify temperatures to be used for specific applications and requirements. Monitoring of the adhesive temperatures is important for optimal results.
Second, the curing of the dispensed material is a temperature dependent process. Curing curves will be available for the various adhesives. In general, higher temperatures will result in faster curing, but too high temperatures can negatively affect the result of the cure.
The curing speed and quality thus depend on adhesive temperature, ambient temperature and PCB temperature.
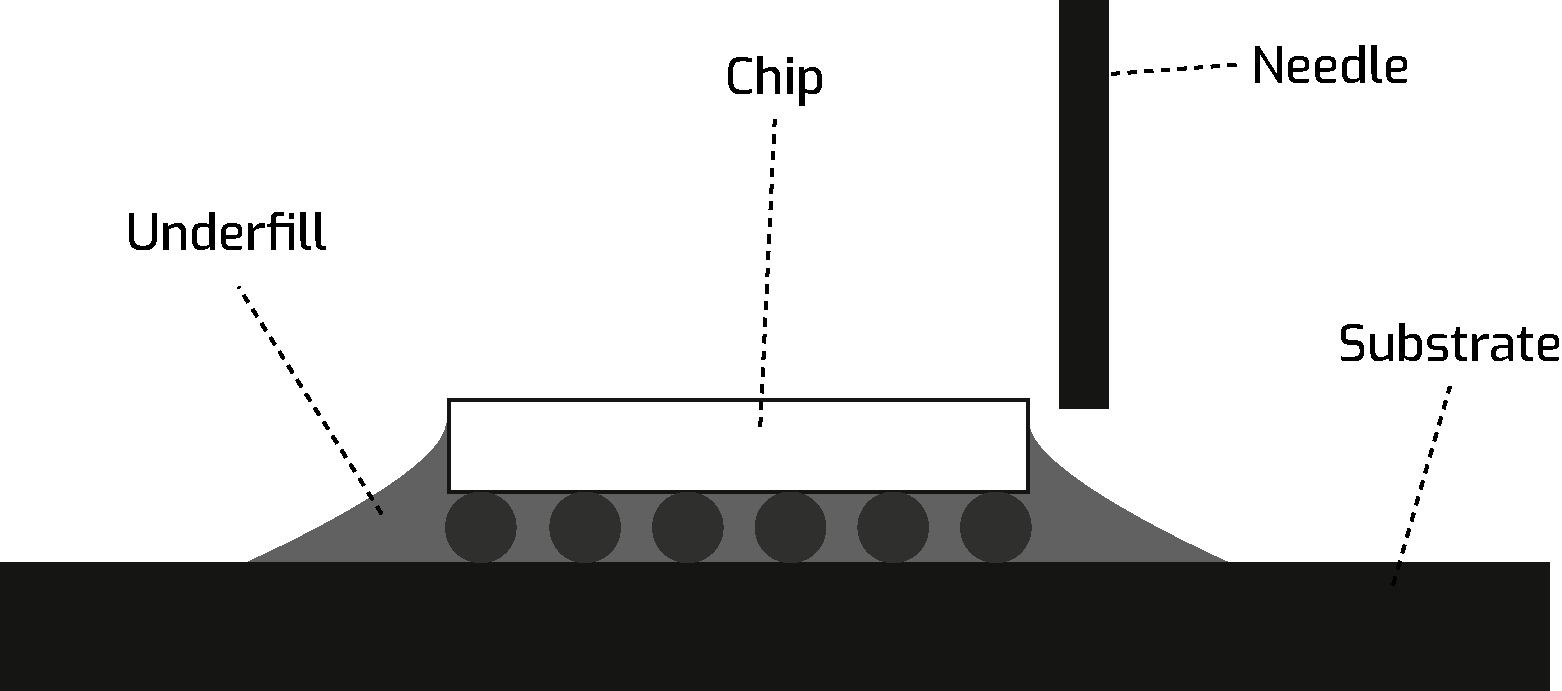
Using Exergen IR sensors to monitor PCBs
To ensure process stability and repeatability, a constant board temperature through the dispense process is critical. Dispensing materials vary in viscosity and filler types, therefore the heat requirement for the board also varies. Measuring the temperature with a contact probe such as a thermocouple or NTC is impossible because of the dynamic nature of the process. Do we need to mention the distance of the non contact sensor? Field of view?
That’s why an Exergens AutoSmart IRt/c non-contact temperature sensor was selected. The Exergens AutoSmart M - measures in “real time” the top-side board temperature which allows the system to provide closed-loop control to maintain the product within the specified temperature range.
The IRt/c sensors provide a closed loop, fail safe means to monitor and control the “top side” board temperature through each of the process zones (pre-heat, dispense heat and post-heat zones), which are typically used during the dispensing process. The passive IR sensors can be configured in any or all three conveyor zones in single or dual lane systems.
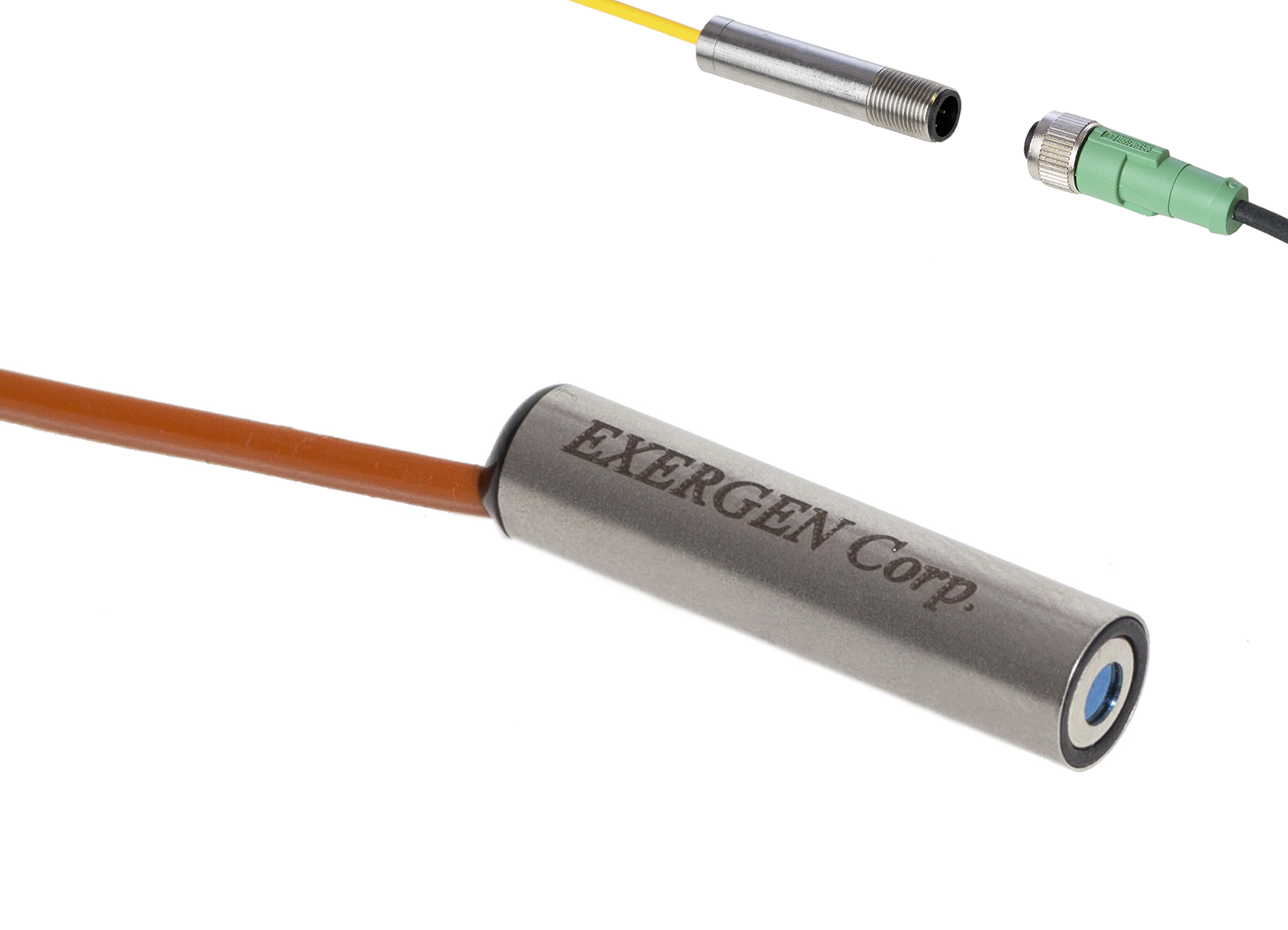
AutoSmart M
They used Exergen’s non contact AutoSmart M, consisting of the smallest available IR sensor, the Micro IRt/c, in combination with the AutoSmart transmitter.
It has the following features:
- Output 0-5V, 0-10V, 4-20mA,
- Repeatability error 0.1% full scale
- Interchangeability ±1.5% full scale
- Resolution approx. 0.1°C
- Very small sensor with a field of view of 4:1
Outcome and advantages of controlling the thermal process
The use of Exergen’s IR sensor increases process control and reduces
- quality and underfill flow and
- curing issues by accurately measuring PCB temperature.
“Controlling the thermal management process in a closed loop is mandatory in a dispensing undersell”, according to Bram Stelt, CEO CleverIR. “We have worked with a broad range of clients in this particular segment and controlling this critical aspect appeared to be the most challenging aspect in this complex heating process”.